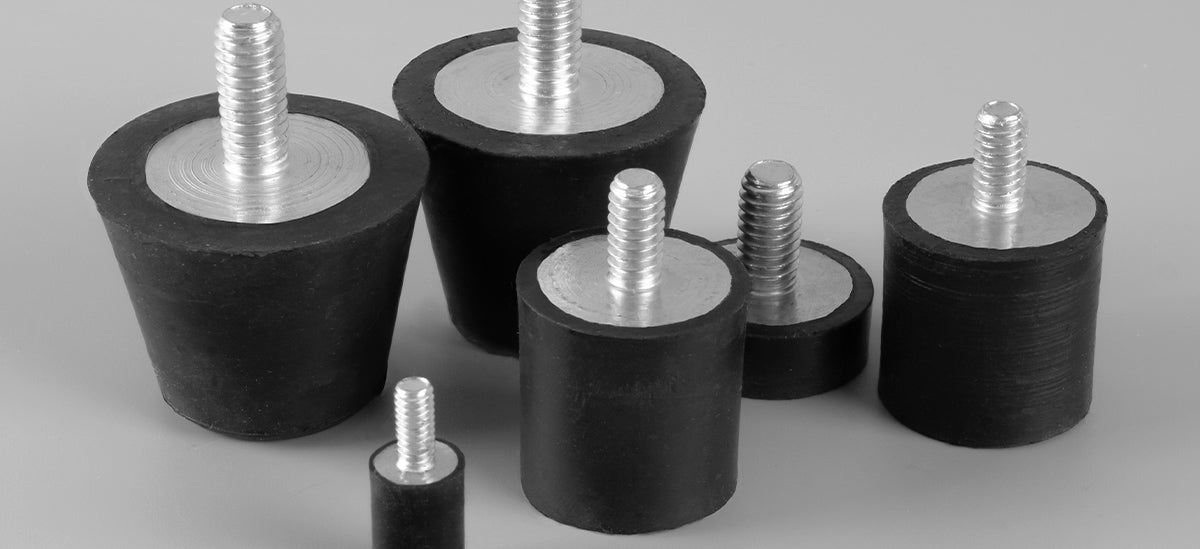
A Simple Introduction to Vibration Isolation
Today’s industrialized world is full of mechanical vibrations and these vibrations are all around us. Transportation, energy, technology, entertainment, communication, healthcare, finance and so much more would jackhammer through our lives each day if not for a simple solution called a vibration isolator.
Simply put, vibration isolators are commonly used in applications where mechanical vibrations occur to dampen those vibrations. Vibration isolators are most often made from bonding various metals and rubber compounds together in a process called vulcanization. The variability of metals and rubber compounds offers flexibility to isolate vibrations properly and withstand the unique environmental conditions each isolator will be subjected to in its application.
Enterprise Rubber, Inc. has specialized in manufacturing vibration isolation mounts for nearly 50 years. Our off-the-shelf parts are manufactured in common sizes and configurations but can also be customized based on the unique requirements of our customers. We manufacture in a variety of compounds, durometers, and mount configurations. Read on for a brief explanation of our most common mount types.
*PLEASE NOTE – Vibration isolation mounts are designed to be used in compression and shear applications and are not recommended when pull-force or torque-force is required. It is your responsibility to determine whether our off-the-shelf parts will work in your application, even when customization or manufacture-to-order occurs.
What Is The Purpose of Vibration Isolation
The purpose of vibration isolation is to reduce or eliminate the transmission of vibrations and shocks from one source to another, typically in mechanical systems or equipment. Vibration isolation serves several essential functions:
Protection: It protects sensitive components, machinery, and equipment from damage caused by excessive vibrations and shocks, extending their lifespan and reliability.
Improved Performance: By isolating vibrations, mechanical systems and equipment can operate more smoothly and accurately, leading to better overall performance.
Comfort: In applications like automotive and construction, vibration isolation enhances the comfort and safety of passengers and operators by reducing the impact of road vibrations or machinery vibrations.
Noise Reduction: Vibration isolation minimizes the transfer of noise associated with vibrations, leading to quieter and more pleasant environments.
Safety: It enhances safety by reducing the risk of structural damage and mechanical failures caused by vibrations and shocks.
Vibration isolation is critical in various industries, including manufacturing, construction, automotive, and aerospace, to ensure the longevity, reliability, and comfort of both equipment and personnel.
What Is an Example of Vibration Isolation
An example of vibration isolation is the use of anti-vibration mounts or isolators in a washing machine. These rubber or elastomeric mounts are placed between the appliance's motor and the machine's frame. When the washing machine is in operation, the motor generates vibrations. The anti-vibration mounts effectively absorb and dampen these vibrations, preventing them from transmitting to the machine's exterior or the floor. This not only reduces noise but also protects the surrounding area from the potentially damaging effects of the machine's vibrations, such as structural damage or discomfort for those nearby.
How do Rubber Vibration Isolators Work?
Rubber vibration isolators play a pivotal role in attenuating vibrations by decoupling the source of vibration from the surrounding environment. Unlike rigid connections, which transmit vibrations efficiently, rubber isolators introduce a compliant element that absorbs and dissipates vibrational energy.
Material Properties of Rubber
Rubber exhibits unique material properties that make it an excellent choice for vibration isolation. Its elasticity allows it to deform under load, effectively absorbing kinetic energy. Additionally, rubber possesses damping characteristics, meaning it can dissipate energy in the form of heat, further attenuating vibrations.
Dynamic Characteristics
Rubber vibration isolators function dynamically, responding to varying frequencies and amplitudes of vibrations. The stiffness and damping properties of the rubber determine its effectiveness in isolating vibrations across different frequency ranges. Furthermore, the design of the isolator, including its shape and geometry, influences its dynamic behavior.
Isolation Mechanisms
Rubber vibration isolators employ several mechanisms to isolate vibrations effectively:
Resilience: Rubber isolators deform under load and spring back to their original shape, absorbing and deflecting vibrational energy in the process.
Damping: Rubber dissipates energy through internal friction as it undergoes cyclic deformation, attenuating vibrations by converting kinetic energy into heat.
Mass-spring system: Rubber isolators function akin to a mass-spring-damper system, where the mass represents the vibrating equipment, the rubber acts as the spring, and damping arises from internal friction.
Rubber vibration isolators serve as indispensable components in the realm of vibration control, offering an effective means to mitigate the detrimental effects of vibrations across diverse applications. Through their unique material properties and dynamic mechanisms, rubber isolators dampen vibrations, enhance equipment performance, and improve overall comfort and safety. As technology advances and engineering challenges evolve, the role of rubber vibration isolators continues to be instrumental in ensuring the smooth operation of machinery and structures in myriad environments.